How Active Magnetic Bearings Work
Operating Principle
A magnetic bearing is an oil-free bearing system that uses electromagnetic forces to maintain relative position of a rotating assembly (rotor) to a stationary component (stator). An advanced electronic control system adjusts these electromagnetic forces in response to forces generated from machine operation.
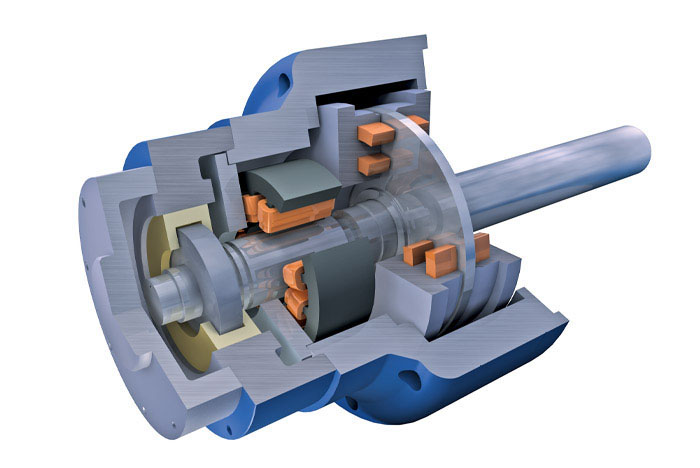
Positioning the Rotor
The radial magnetic bearing positions the rotor using four electromagnets, each comprised of a stator component and a rotor component. Opposite electromagnets are adjusted to pull against one another.
When an external force causes the rotor to change position, the movement is identified by position sensors. The electronic control system responds by adjusting the current flowing through the respective electromagnets – returning the rotor to its original position.
The axial magnetic bearing positions a rotor axially using electromagnetic forces pulling in opposition on the collar.
Supplemental Support
Due to the sensitive nature of magnetic surfaces, active magnetic bearing systems include auxiliary bearings. These bearings support the rotor when the machine is stationary, as well as accommodate overloads and support the rotor in the event of system fault.
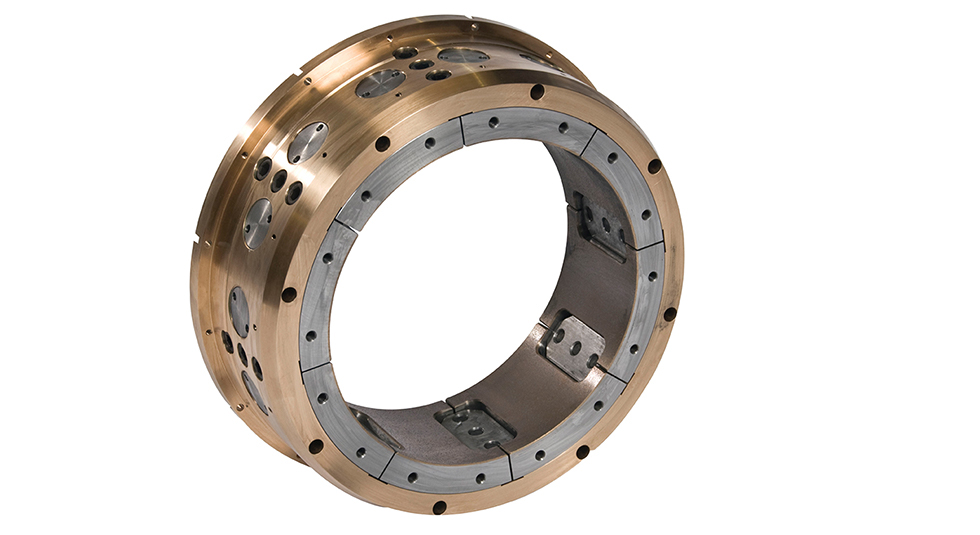
Advantages of Magnetic Bearings
- Improved safety, environmental benefits and elimination of ancillary equipment resulting from the elimination of the oil system
- Optimized rotordynamic control
- Variable speed operation
- Inherent diagnostic capabilities
- Low energy consumption
- High reliability and availability
- Virtually maintenance free
- Lower noise emissions
- Reduced infrastructure costs, including the possibility of outdoor installations
- Reduction of total life cycle costs
Typical Applications
Explore the Life-Cycle Cost Savings of AMBs
Advanced AMB technologies eliminate auxiliary equipment, lower energy consumption, minimize maintenance, and maximize reliability, providing cost savings throughout the life-cycle of your machinery