Case Study
Groningen: 17 Years and 20 Installations Later
Groningen, Europe’s largest natural gas field, was discovered in 1959. Located in The Netherlands, production began in 1963 and depleted nearly 50 percent of its reserves by the end of the decade. NAM (Nederlandse Aardolie Maatschappij), a joint venture between Royal Dutch Shell and ExxonMobil, originated in the mid-1990s. Its goal was to find the most cost-effective way to extract the gas and extend the life of its reserves, ensuring the gas field could continue to supply the region.
The challenging parameters of the project were to provide availability of at least 87% and produce a low total cost of ownership. By following these parameters and upgrading the equipment, including the motors and compressors, the gas field could supply gas to all of The Netherlands, Germany and Belgium for an additional 40 years.
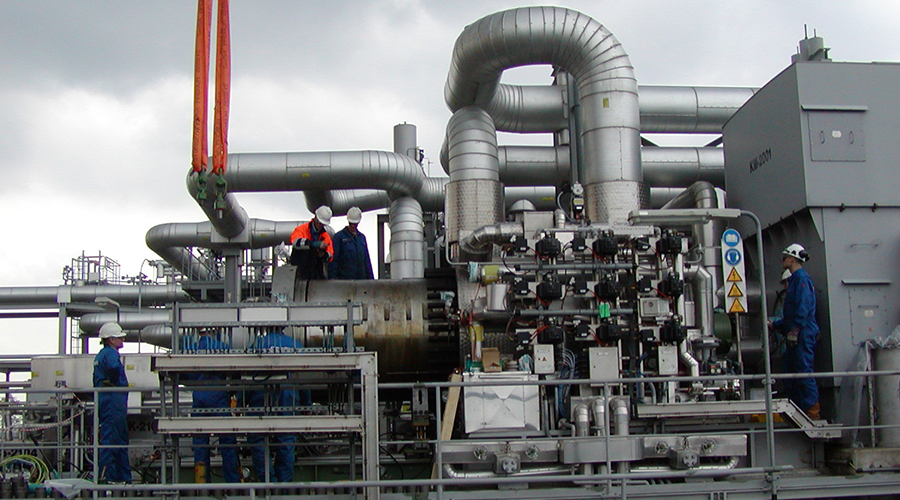
Henk Niezen, Project Director, and Wim de Groot, Rotating Equipment Engineer of NAM GLT, share their experience working on the NAM project and their decision to implement a compression string using magnetic bearings systems provided by Waukesha Magnetic Bearings.
Solving the Challenge
User requirements were for high reliability, high energy efficiency, low maintenance and low investment cost across a wide compressor speed range with minimal vibration and noise.
Waukesha Magnetic Bearings partnered with Siemens to initially install three radial active magnetic bearings for the motor, two radial magnetic bearings and an active magnetic thrust bearing on the compressor, and a digital controller with analog amplifiers.
There have been a total of 20 installations since the initial installation. Waukesha Magnetic Bearings has produced the bearings for every installation even though the machines have varied significantly in terms of number of stages, hence the dynamics of the rotor. Waukesha Magnetic Bearings was able to adjust for these differences through software in the controllers.
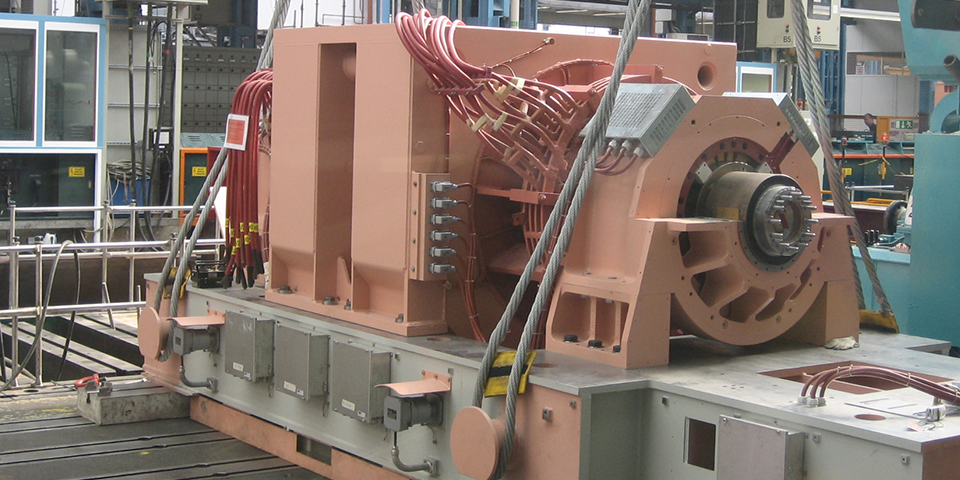
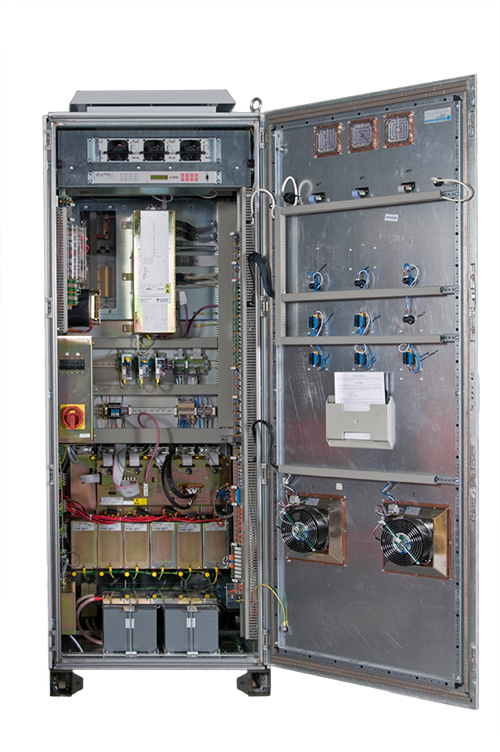
Application Details
- Natural gas compression, extracting gas from underground wells utilizing 23 megawatts of electric power
- 3 radial active magnetic bearings for the motor
- 2 radial magnetic bearings and 1 thrust bearing on the compressor
- 1 digital controller with analog amplifiers
Advantages
- Proven availability exceeds 99.9% over 20 installations
- Lower life cycle cost, from initial installation through continuing operating costs
- Minimal maintenance costs
- Complete versatility to operate throughout the speed range from very low speed to high speed with good vibration control
- Environmentally friendly – cleaner, more efficient design