News
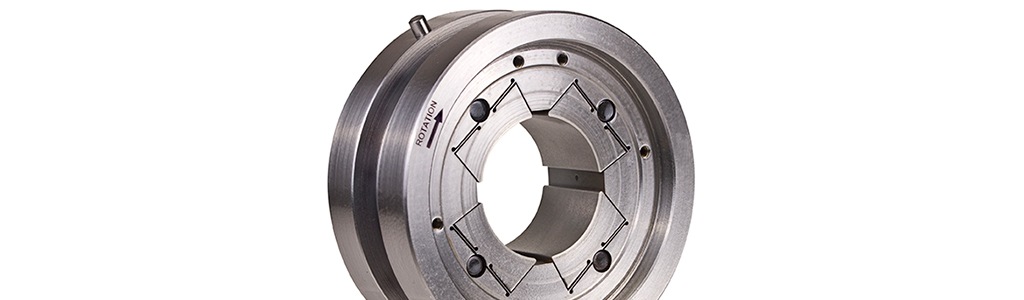
Bearing Design Reduces Performance Variability
Tight-tolerance tilt pad journal bearings provide increased stability in high speed turbomachinery equipment
By Dr. Kenneth R. Bischof
Published in International Oil & Gas Engineer, 2009
As machinery builders strive for improved efficiency, higher pressure ratios or increased operational flexibility, static performance and rotordynamic challenges become even greater for rotor-bearing system engineers. Often these challenges are a direct result of a more flexible rotating system and increased rotor length, leading to increased bearing spans.
To combat these challenges, fluid film bearing engineers have traditionally relied on a variety of features within a tilt pad journal bearing, such as assembled clearance, pad-angle, pre-load and pivot offset. When traditional feature variations are not sufficient for more challenging systems, bearing structural stiffness and damping have also been improved through the use of higher performing ball-and-socket pivot designs as well as employing squeeze-film dampers, respectively.
System rotordynamic challenges have placed an increased emphasis on reliably maintaining tight tolerances within bearing manufacturing processes. Even the slightest tolerance variations can have dramatic impact on bearing stiffness and damping characteristics, ultimately leading to differences between predicted and actual performance of the machine.
Early in 2008 Waukesha Bearings completed development of a new bearing design aimed at solving many of the technical issues surrounding the dynamic performance of the rotor-bearing system. This new design utilises a patent-pending, single-piece frame construction with the tilt pads integral to the shell and without sacrificing pivot stiffness, creating a potential fatigue-failure point or restricting free-tilt of the journal pads. This is accomplished through the use of an EDM manufacturing process used in combination with a hardened steel pivot, offering a solution with reduced pad flutter, particularly in unloaded pads, and less vibration, fatigue and wear. The bearing is also designed with a secondary integral pad stop that prevents over-rotation as well as improved oil distribution across the pads.
To read the complete article, download the PDF below.