Bearing Damage Index
Black Scab / Wire Wool
A large dirt particle (probably not less than 1 mm [0.04″] across) carried into the clearance space by the lubricating oil and becoming embedded in the bearing may form a hard scab of material by contact with the steel journal or thrust collar. This scab will then cause severe damage to the mating steel surface, which is machined away – cut into so-called ‘wire wool’.
Susceptibility to scab formation depends on the nature of the lubricant and the composition of the steel of the rotor shaft or collar. Steels containing chromium or manganese in excess of 1% appear to be particularly susceptible to scab formation, especially in high speed machines with bearing rubbing speeds over 20 m/s (4000 ft/min) and with oils containing extreme pressure additives.
Addressing the Damage
Since black scab damage is self-propagating once started, bearings showing such damage should be replaced with new bearings.
Pay particular attention to cleanliness during assembly, taking care to avoid contamination of the bearing surface and oil ways by swarf or other contaminants.
The possibility of changing the journal or collar surface material by sleeving with mild steel or hard chrome plating should also be investigated. Changing the bearing alloy is unlikely to be effective.
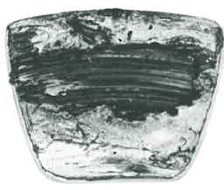
Figure 1: ‘Black scab’ formation on whitemetal-lined thrust pad

Figure 2: Tin-based whitemetal tilt pad thrust bearing with formation of black scab
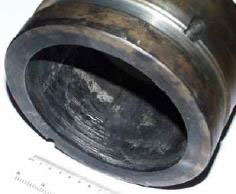
Figure 3: Tin-based whitemetal radial bearing showing formation of black scab
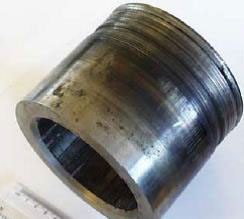
Figure 4: Steel shaft sleeve running in Figure 3 bearing, showing severe machining damage