‘Directed Lubrication’
Industry-Leading Lubrication Method
‘Directed Lubrication’ from Waukesha Bearings, available on tilt pad thrust and journal bearings, reduces power loss and bearing temperatures for increased load capacity and improved bearing performance.
Developed by us in the 1960s, ‘Directed Lubrication’ is now an industry standard. ‘Directed Lubrication’ controls oil flow through the use of nozzles or oil jets, introducing fresh oil to each pad.
Waukesha’s design has been more fully proven over a longer period than any other product subsequently developed and aiming to achieve similar results.
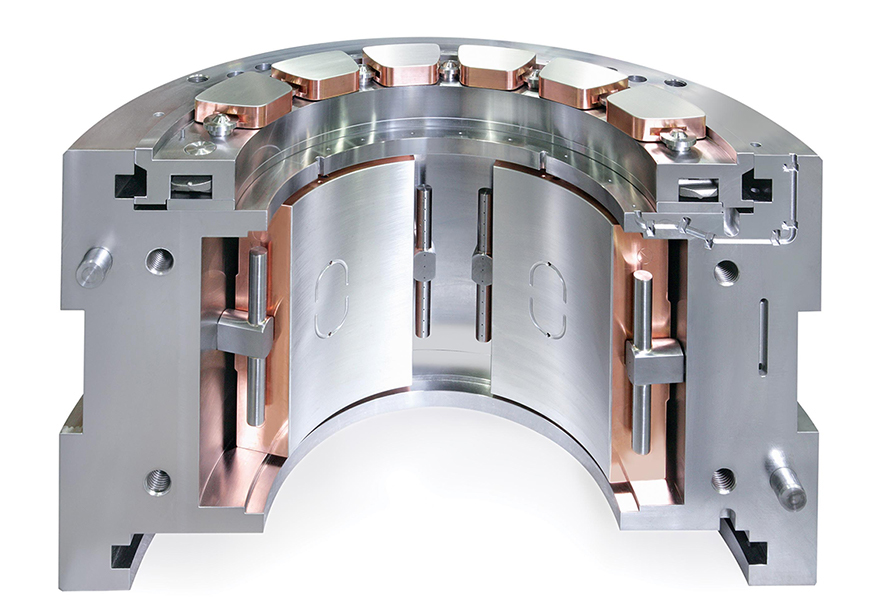
‘Directed Lubrication’ Thrust Bearings
In tilt pad thrust bearings, ‘Direction Lubrication’ can significantly reduce power loss and oil flow, particularly at high speeds, by eliminating churning of the oil within the casing that results in high power loss in flooded lubrication systems. The thrust bearing housing must be kept free of bulk oil by ample drain area around the collar periphery. No shaft seals are required, thus also simplifying installation.
Our ‘Directed Lubrication’ has oil jets, which impinge on the trailing edge of the proceeding pad to help reduce local high temperatures, scour hot oil from the collar as well as spray fresh oil to the inlet edge of each pad. By reducing hot oil carryover, Waukesha’s ‘Directed Lubrication’ reduces pad temperatures and also increases film thickness, permitting higher specific loading. This allows the use of a smaller bearing to support a given load, leading to further saving in power due to a reduced bearing diameter.
Key Benefits in Thrust Bearings
- Significantly reduced power loss – often over 50% at high speeds
- Reduced bearing surface temperatures
- Lower oil flows at high speeds
- Increased oil film thickness
- Increased load capacity
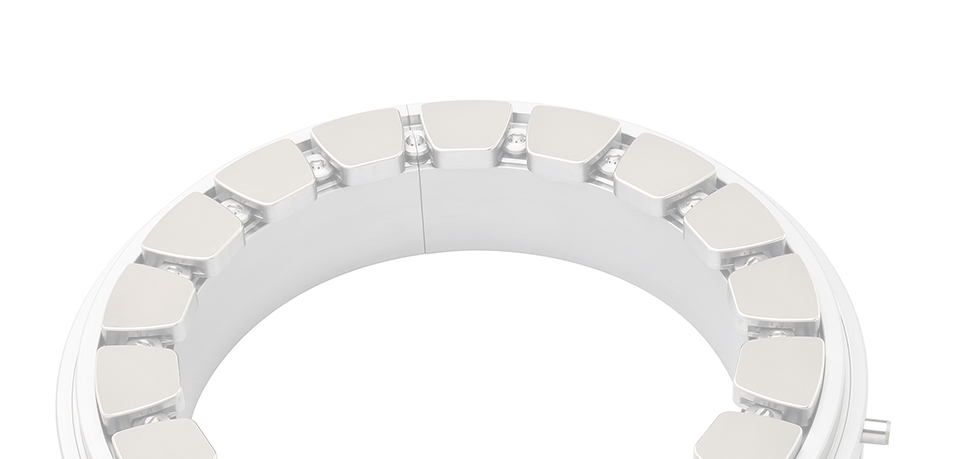
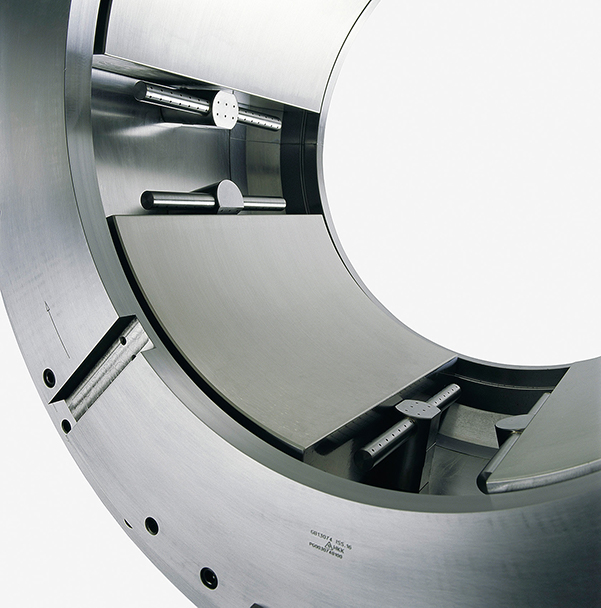
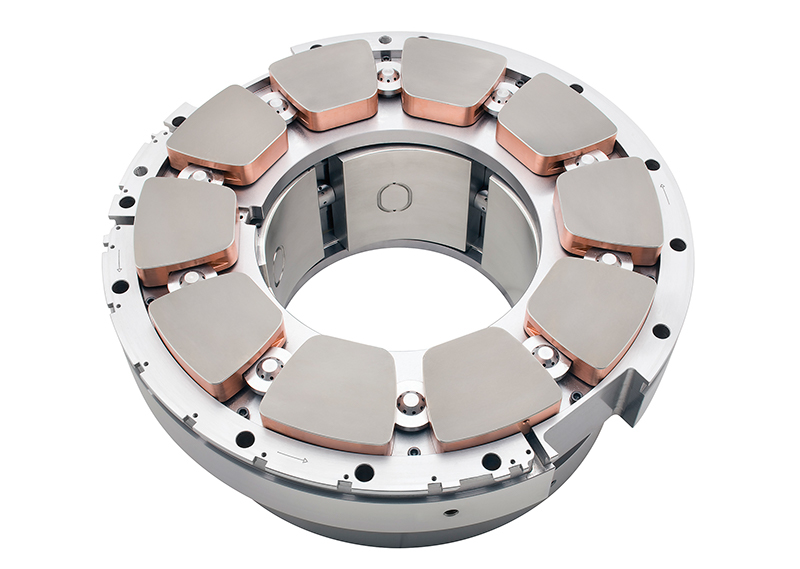
How Oil Flow Affects Power Loss
Power loss in a bearing results from the combination of viscous shear in the oil film and (in flooded bearings) turbulence in the oil caused by the rotation of the shaft in an oil filled housing. This power loss appears as heat, and this must be removed from the bearing by the flow of lubricant.
Contact Waukesha Bearings for assistance in evaluating power loss and the oil flow required.
Trailing Edge Cooling
As part of a ‘Directed Lubrication’ system, trailing edge cooling can further lower bearing temperatures.
The patented design features grooves in the trailing edge face of the tilting pad and a spray bar adjacent to the trailing edge to deliver cooling flow. The grooves increase the surface area and allow the lubricant to penetrate deeper into the pad for greater cooling effect.
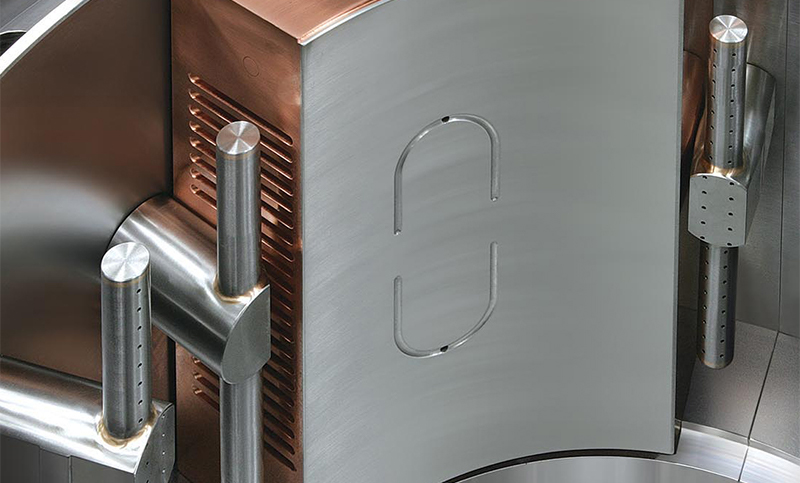
Downloads
- Experimental Comparison of Flooded, Directed and Inlet Orifice Type of Lubrication for a Tilting Pad Thrust Bearing (Journal of Lubrication Technology, 1972)
- Influence of Oil Injection Method on Thrust Bearing Performance at Low Flow Conditions (Proceedings of the 28th Turbomachinery Symposium, 1999)