Hydrodynamic Bearings
High-Performing Hydrodynamic Bearings
Hydrodynamic bearings are widely used in high-performance machinery to provide reliable operation over extended periods of time. Hydrodynamic bearing operation is largely non-contacting, providing theoretically infinite life when properly designed and maintained.
These bearings play a critical role in the operation of equipment found in power generation plants, oil refineries, petrochemical plants and other process plants, and in large marine propulsion machinery.

Hydrodynamic Bearing Requirements
Hydrodynamic bearings require three elements to generate the hydrodynamic film:
- Viscous fluid (the lubricant)
- Relative motion (the sliding action of one surface relative to another)
- Converging geometry
In journal bearings, the converging geometry is provided by the slight difference in diameters of the shaft and the bore of the bearing. For improved static and dynamic performance, a defined profile can be machined into the bearing. Tilt pads are often used if stability is an issue, if varying conditions must be accommodated or if other bearing performance parameters require optimization.
In thrust bearings, the converging geometry is either machined into the face of a fixed plate or provided by the tilting action of tilt pad thrust bearings. A fixed geometry is designed for a specific condition, while tilt pad bearings are often used to accommodate changing conditions.
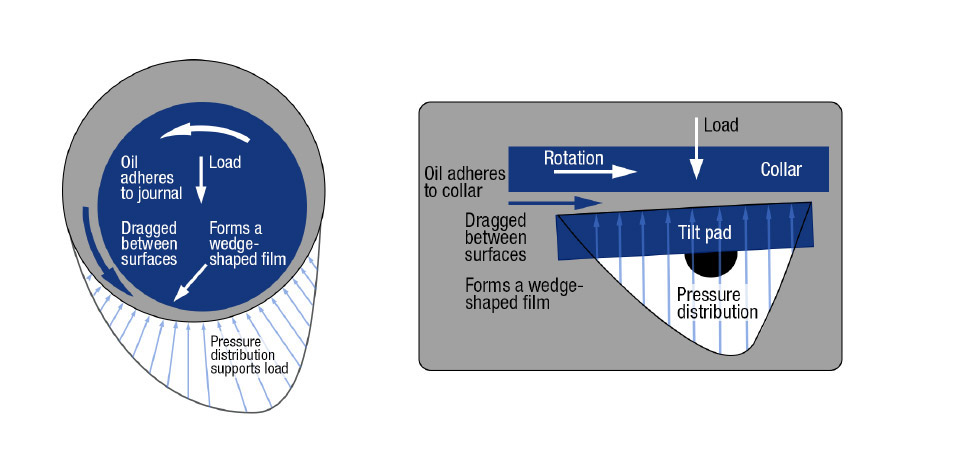
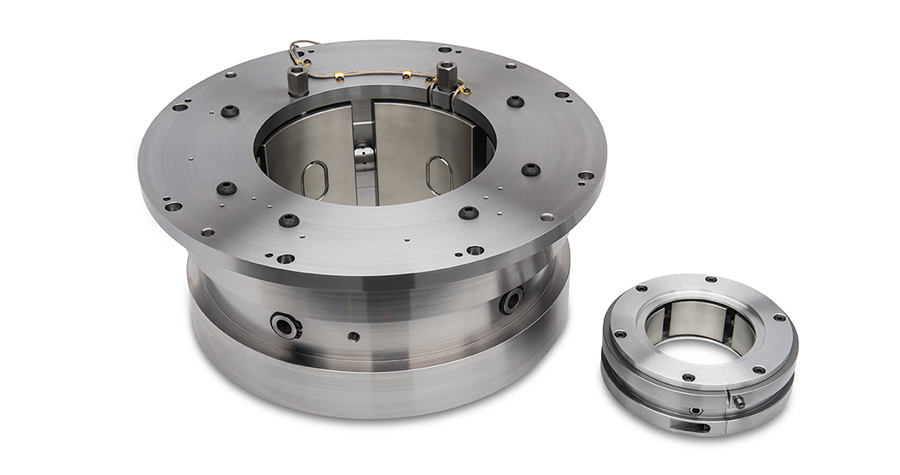
Hydrodynamic or Fluid Film?
While “hydrodynamic” and “fluid film” are often used synonymously, fluid film bearings also include hydrostatic bearings.
Hydrostatic bearings use an external source to supply the necessary film pressure between surfaces. Hydrodynamic bearings generate the pressure through the relative motion of the surfaces and the converging geometry.
Waukesha Bearings specializes in hydrodynamic fluid film bearings, but may also incorporate features of hydrostatic bearings. A primary advantage of hydrostatic bearings is the ability to generate a separating oil film without relative motion of the bearing surfaces. A hydrostatic lift feature incorporated into a hydrodynamic bearing design provides a separating film prior to shaft rotation. This prevents contact of surfaces at start-up and the potential damage which might occur to the surfaces of heavily loaded bearings as they go through the boundary and mixed film regimes.
Journal Bearings
Waukesha Bearings custom engineers hydrodynamic bearings in a variety fixed profile and tilt pad designs. Bearing geometry and materials are carefully considered to provide minimum power loss and optimum dynamic performance for the given operating conditions.
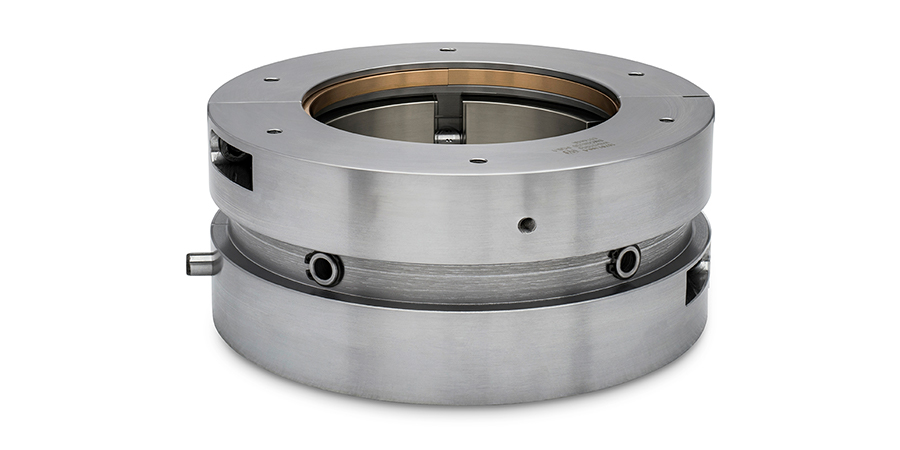
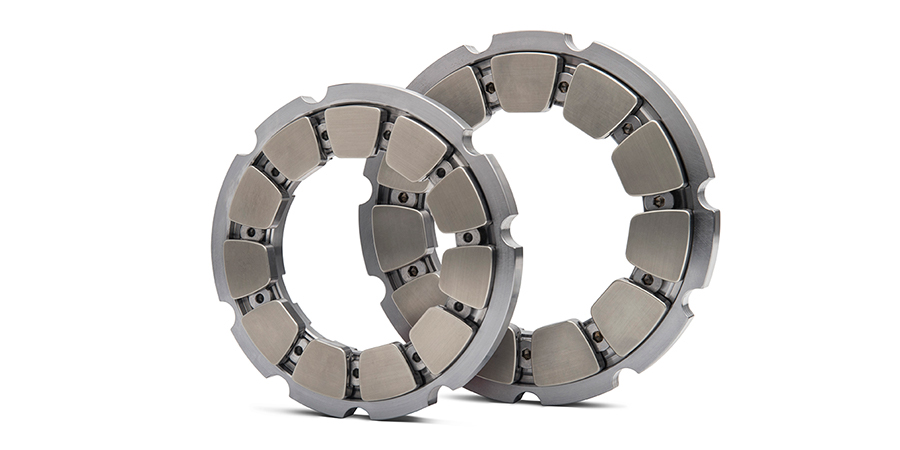
Thrust Bearings
Waukesha Bearings offers fixed profile hydrodynamic thrust bearings for lightly loaded applications and advanced tilting pad solutions for more demanding operating conditions.
Tilt pad designs may be non-equalizing or self-equalizing with flooded or ‘Directed’ lubrication to support the equipment’s unique requirements.
The Role of Bearings
The primary functions of bearings are to control the rotor position, balance forces on the system, and provide damping.
Journal bearings support radial loads (perpendicular to the axis of rotation). Thrust bearings support axial loads (along the axis of rotation).
The materials and design of thrust and journal fluid film bearings are selected to optimize the bearing geometry for increased efficiency of the equipment and fewer demands on ancillary equipment.
Rolling Element Bearings
Instead of a shear layer of film between the two surfaces, rolling element bearings use balls, rollers or needles to allow relative motion between two surfaces. Typically, large machinery and machinery operating at high speeds and loads require the performance characteristics of hydrodynamic bearings.